Masseaufbereitung
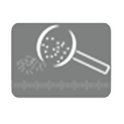
Masseaufbereitung
Die Masseaufbereitung von firmeneigenen und kundenspezifischen Keramikpulvern erfolgt je nach Formgebungstechnologien auf beheizten Kugelmühlen bzw. Knetern und stellt somit den Ausgangspunkt von Keramikteilen dar.
- Kugelmühle
- US-Mischer
- Kneter
- Scherwalze
Formgebung
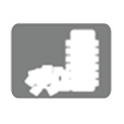
Formgebung
Für die Herstellung von Hochleistungskeramik stehen verschiedene Formgebungstechnologien zur Verfügung:
LP-CIM
Das Abformungsverfahren Heißgießen, auf der Basis von Wachsbindermischungen, erfolgt bei einem Druck von 1 bis 6 bar mit anschließender hydraulischer Nachverdichtung. Durch den niedrigen Druck im Einfüllprozess und die damit verbundenen geringen Einspritzkräfte können filigrane, dünnwandige, kleine Konturen erzeugt werden.
HP-CIM
Anders als beim Heißgießen wird im Hochdruckspritzguss bei dem Formfüllungsprozess mit einem Einspritzdruck von 400 bis 2000 bar gearbeitet. Die höhere Grünfestigkeit des Spritzlings ermöglicht ein automatisiertes Handling des Formgebungsprozesses in der Serienfertigung.
Schlickerguss
Beim Schlickerguss handelt es sich um ein Formgebungsverfahren, für Hohlkörper wie Tiegel, welches mit Hilfe einer porösen, wassersaugenden Form (meist aus Gips) einer wässrigen Suspension bzw. einem Schlicker das Wasser entzieht. Dadurch lagert sich der Feststoff an der Form ab und es bildet sich der sogenannten Scherben, das spätere Teil.
Pressen
Im Haus stehen uniaxiale und isostatische Pressen zur Herstellung von Formkörpern zur Verfügung. Die Verarbeitung von Keramik-Granulaten für 2-D bzw. 2½ D Formkörpern, erfolgt bei einem Pressdruck von bis zu 100MPa.
- Uniaxial
- Isostatisch
Grünbearbeitung
Für die Herstellung von Funktionsmustern und dickwandigen Keramikteilen kommen modernste CNC-gesteuerte Maschinen zum Einsatz. CAD/CAM-Systeme tragen zu der Optimierung von Bauteil-Geometrien und Bearbeitungsstrategien in der Prototypenfertigung bei.
Thermische Prozesse
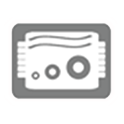
Thermische Prozesse
Oxidierend-brennende Aggregate als auch Anlagen mit Schutzgas bzw. Vakuumbetrieb stehen für den Entbinderungs- bzw. Sinterprozess zur Verfügung. Die verwendeten Prozessparameter in Kombination mit dem Grundmaterial sind entscheidend für die Ausbildung der Keramikeigenschaften.
- Oxidierende Atmosphäre
- Unter Schutzgas
Hartbearbeitung
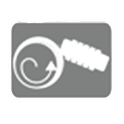
Hartbearbeitung
Die Grenzen der Formgebungstechnologien machen es teilweise notwendig, CNC-gesteuerte Rund- und Flachschleifmaschinen für die Nachbearbeitung (Passungen, Anguss,…) von Keramikteilen einzusetzen.
Für die gezielte Herstellung von Funktionsoberflächen stehen Läpp-, Polier- und Bürstmaschinen zur Verfügung.
- Flachschleifen
- Rundschleifen
- Gleitschleifen
- Honen
- Polieren
- Läppen
Baugruppenfertigung
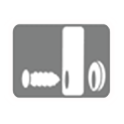
Baugruppenfertigung
Die Grenzen der Herstellungstechnologien bzw. der Materialeigenschaften von Keramikbauteilen machen es notwendig, diese mit anderen Materialien zu kombinieren. Die TKC-Technische Keramik GmbH bietet zusätzlich zu der Fertigung von Keramikteilen auch Funktionsbaugruppen an. Schwerpunkt dabei ist die Herstellung von vakuumdichten Metall-Keramik-Verbunden, welche durch Aktiv-Hart-Löten hergestellte werden.
Qualitätskontrolle
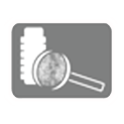
Qualitätskontrolle
Die Qualitätssicherung der Produkte erfolgt nach Absprache mit dem Kunden. Neben der Überwachung von Maßen, Form- und Lagetoleranzen können im firmeneigenen Labor Dichte, Porosität, Rauigkeit und Kristallitgröße bestimmt werden. Die Reinigung der Keramikteile erfolgt über eine automatische, ultraschallunterstützte Waschstraße. Anschließend werden die Bauteile versandfertig verpackt.
Wir sind seit 2010 als TKC und vorher bereits im Firmenverbund durchgehend nach ISO 9001 und ISO 13485 zertifiziert.